Salzgitter AG and VNG AG cooperate in the field of green gases
VNG AG and Salzgitter AG will jointly test the use of climate-neutral hydrogen and biomethane for steel production at the Salzgitter Flachstahl GmbH plant in Salzgitter, Lower Saxony. A memorandum of understanding has been signed on this.
The vision of the two companies is to supply the integrated steelworks in Salzgitter, Lower Saxony, with ‘turquoise hydrogen’ produced in central Germany via a pipeline. The first step was to assess the economic viability by means of a feasibility study carried out jointly with the Fraunhofer Institute for Energy Infrastructures and Geothermal Systems IEG and the Fraunhofer Institute for Systems and Innovation Research ISI. The focus was on the possible use of the pyrolysis process for hydrogen production.
“We have come to the conclusion that, based on the scenarios we’ve examined, the production costs of hydrogen from the pyrolysis process can be competitive with electrolysis and that the process can be helpful in the low-emission production of hydrogen. However, the prerequisite is that the technological challenges of pyrolysis are solved promptly, good uses are found for the resulting carbon and methane emissions are limited along the entire process chain in a transparent way,” said Prof. Mario Ragwitz, who heads the Fraunhofer Research Institution for Energy Infrastructures and Geothermal Systems (IEG) based in Cottbus.
The economic viability of the large-scale industrial use of the pyrolysis process was examined, taking into account various political framework conditions and necessary investments for the pyrolysis plant, transport routes and the use of a storage facility. The scenarios differed with variation of the CO2, electricity and gas price as well as biogas use. In addition, a comparison was drawn with the use of solely natural gas or the use of the electrolysis process for hydrogen production with electricity produced in Germany. Furthermore, the incorporation of Salzgitter in a future hydrogen network also played a role.
“The study has shown that supplying the Salzgitter site with green gases is technically and economically feasible despite the expected high demand for hydrogen,” said Cornelia Müller-Pagel, who heads the Green Gases division at VNG AG, headquartered in Leipzig. “With a view to economic viability, however, we need an even greater openness to technology in the short and medium term when developing the hydrogen economy, including in funding policy. In addition to green hydrogen, blue and turquoise hydrogen should also play an equal role in the future.” In order to be able to better compare the different production methods of hydrogen with regard to their environmental compatibility in the future, Müller-Pagel also advocates a monitoring and certification system that is as uniform as possible and that should be used throughout the EU.
At Salzgitter AG, the examination of the future use of hydrogen in production goes hand in hand with the analysis of modern methods and innovative process technologies in order to significantly reduce CO2 emissions: A concept for decarbonising steel production was developed back in 2015 under the project name SALCOS (Salzgitter Low CO2 Steelmaking). The first steps in the implementation of this concept are the PEM electrolysis with a capacity of 2.5 megawatts, which is currently under construction, and a high-temperature electrolyser with a capacity of 720 kilowatts on the factory premises to cover the current hydrogen demand for annealing processes internally, as well as the construction of seven wind turbines.
Dr. Alexander Redenius from Salzgitter AG: “The transition to decarbonised steel production is a major challenge. International competitive pressure and the enormous transformation costs make state support essential. In addition, we advocate a gradual transformation of the conventional steel production process. In the short term, CO2 savings of more than 60 per cent could be achieved by using natural gas in a new direct reduction unit to be built compared to the conventional route. By gradually adding up to 100 per cent hydrogen, steel can be produced in an almost CO2-neutral way. This could happen hand in hand with the development of generation capacities for green and turquoise hydrogen.”
The partners now want to define further possible steps in a follow-up project and therefore create the basis for the joint implementation of the project idea.
About Salzgitter AG
Salzgitter AG is one of the leading steel and technology groups in Europe – with external sales of around EUR 9 billion, over 25,000 employees and almost 160 national and international subsidiaries and affiliates. It is divided into the business units of Strip Steel, Plate/Section Steel, Mannesmann, Trading and Technology. Salzgitter Flachstahl GmbH is the largest subsidiary. It produces a wide range of high-quality special and branded steels for demanding customer sectors such as the automotive industry.
More information can be found online at: www.salzgitter-ag.com. Information about the SALCOS project can be found at: https://salcos.salzgitter-ag.com/.
Press pictures
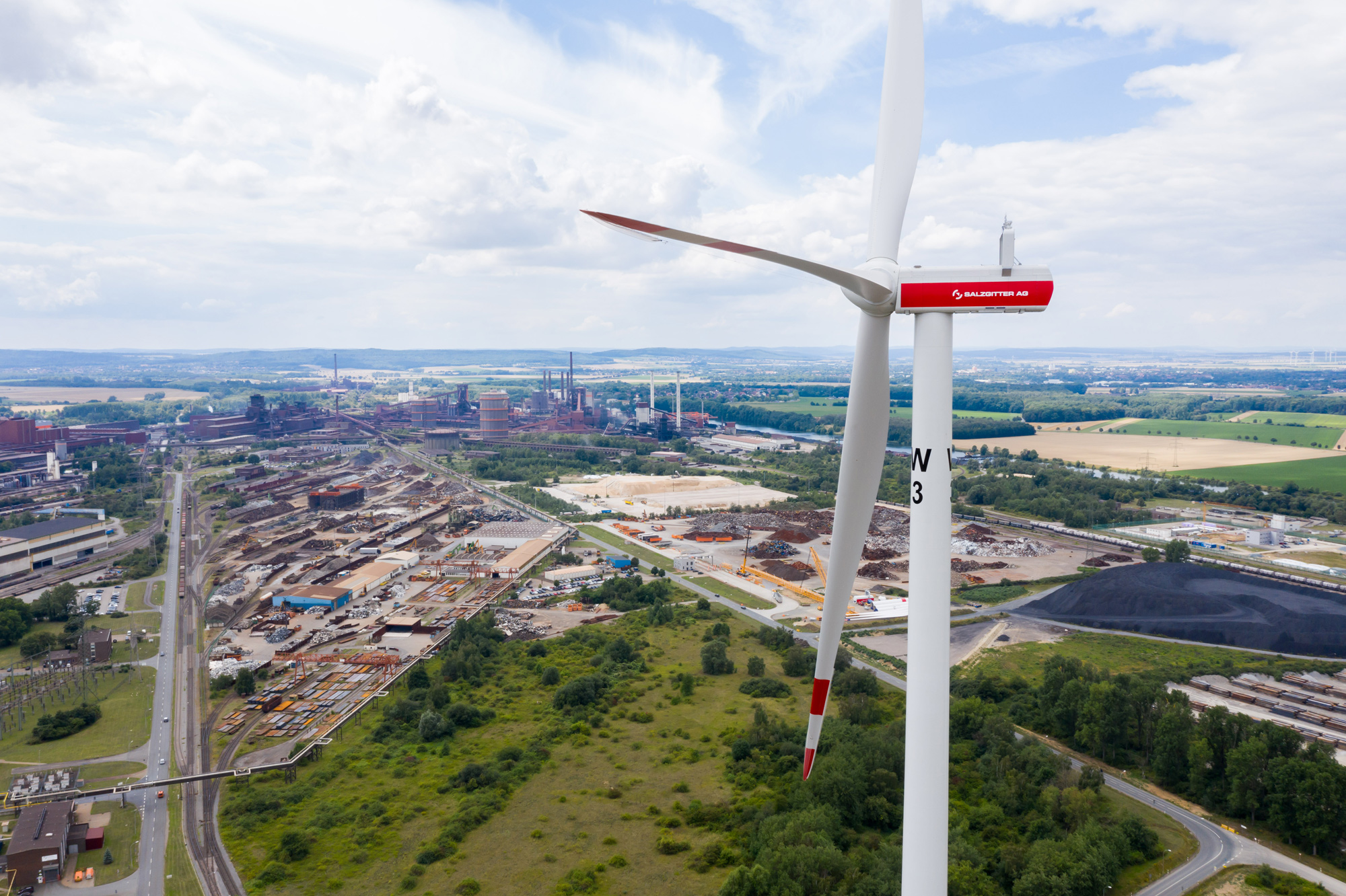
Facility from Salzgitter AG in Salzgitter, Lower Saxony (© Salzgitter AG)